Технологии изготовления шестигранных прутков
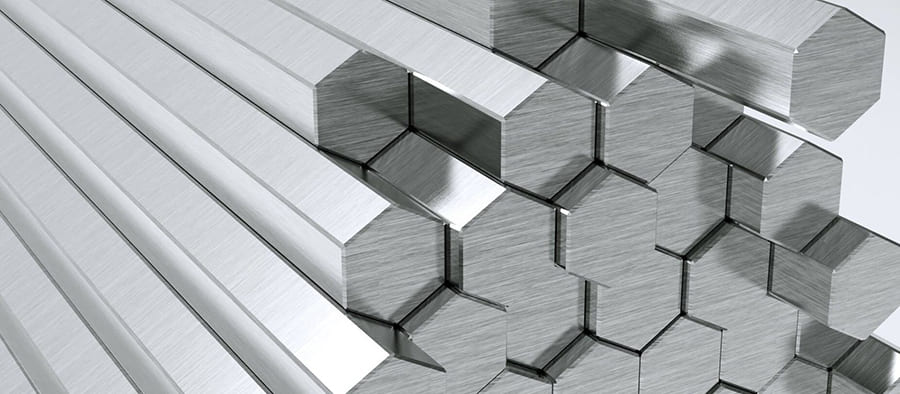
Разработка промышленной технологии изготовления шестигранных прутков размером «под ключ» из высоколегированных, в том числе труднодеформируемых марок стали на Златоустовском металлургическом заводе в термокалибровочном цехе (ТКЦ).
1.СОСТОЯНИЕ ВОПРОСА И ЦЕЛЬ ИССЛЕДОВАНИЯ.
В настоящее время в общем объёме производства калиброванной стали в ТКЦ более 20% составляют холоднотянутые прутки шестигранного профиля. Марочный сортамент представлен преимущественно конструкционными углеродистыми и легированными сталями ( ГОСТ 1050-81,4543-71), а также автоматными (ГОСТ 1414-75); меньшая доля приходится на нержавеющие хромоникелевые стали типа 08-12Х18Н10Т. Диапазон изготавливаемых размеров «под ключ» изменяется в пределах 10-41 мм. В 2001 году марочный сортамент усложнился с появлением в заказах марок ЭИ268, ЭП288, ЭИ961, ЭП56, ЭП33,ЭИ107 и др., расширился размерный сортамент в сторону мелких профилей (5-9 мм).На ряде позиций изменились требования заказчиков к состоянию поставки металла, вместо термообработанного – нагартованное с нормированными характеристиками механических свойств и твёрдостью.
Необходимость выполнения указанных заказов потребовала создание новой технологии и усовершенствования действующей. Использование опыта других заводов показало, что весьма эффективным и перспективным является способ формирования фасонного профиля; в т.ч. шестигранного , в роликовых клетях. Опытно-промышленное опробование изготовления шестигранных прутков размером «под ключ» 8-10 мм ( из мотков) на линии 2КЛ-40Б с использованием 4-х роликовой клети конструкции ЧПТУ подтвердило экономическую целесообразность освоения этой технологии, в том числе и на цепных волочильных станах. Применение клетей взамен монолитных волок позволяет сократить количество протяжек и отжигов, снизить трудоёмкость изготовления.
На основании вышеизложенного целью настоящего исследования является:
- Разработка промышленной технологии изготовления шестигранных прутков размером « под ключ» 10-36 мм из высоколегированных нержавеющих, в том числе труднодеформируемых марок сталей.
- Уточнение технологических маршрутов волочения шестигранных прутков, поставляемых в нагартованном состоянии.
- Интенсификация прцесса холодного деформирования металла за счёт применения неприводных калибрующих роликовых клетей взамен монолитных волок.
2. МЕТОДИКА ИССЛЕДОВАНИЯ
Объектом исследования являлся прутковой и мотковой подкат круглого сечения, калиброванные шестигранные прутки стали марки 12Х18Н10Т и мотки на всех стадиях их изготовления из нержавеющих и конструкционных марок стали.
Опыты по изготовлению шестигранных прутков проводились на промышленном оборудовании ТКЦ. Для исследования качества опытного металла применялись следующие стандартные методы исследования:
- измерение твёрдости;
- испытание механических свойств;
- микроанализ;
- измерение геометрических размеров профиля.
3.ЭКСПЕРИМЕНТАЛЬНАЯ ЧАСТЬ
3.1. Разработка промышленной технологии изготовления шестигранных прутков размером «под ключ» 10-36 мм из высоколегированных марок стали. С учётом имеющегося пакета заказов ( в том числе для МАП) на калиброванные прутки шестигранного сечения сформировался определённый марочный сортамент, представленный высоколегированными марками сталей разного структурного класса (таблица 1).
Таблица 1
Перечень марок, осваиваемых для производства шестигранной стали.
Марка стали |
Структурный класс |
НТД на поставку ( ТУ, ГОСТ) |
08-12Х18Н9(10)Т |
Аустенитный |
ГОСТ 5949-75, ТУ 14-1-3957-85 |
10Х11Н23МР-ВД (ЭП 33ВД) |
Аустенитный (дисперсионно-твердеющая с интерметаллидным упрочнением) |
ТУ 14-1-3957-85 |
07Х16Н6-Ш (ЭП 288-Ш) |
Аустенито-мартенситный |
ТУ 14-1-759-78 |
14Х17Н2 (ЭИ 268) 12Х13 |
Мартенсито-ферритный |
ГОСТ 5949-75, ТУ 14-1-3957-85 |
20-40Х13 13Х11Н2В2МФ (ЭИ 961) |
Мартенситный |
ГОСТ 5949-75 ТУ 14-1-1791-76 ТУ 14-1-3564-83 ТУ 14-1-3957-85 |
Поэтому необходимо было освоить технологию изготовления шестигранных прутков из вышеперечисленных марок стали, обеспечивающую качество металла в соответствии с требованиями НТД на поставку, в том числе по заказам МАП.
При освоении технологии производства прутков возникли трудности связанные:
- с обеспечением качества поверхности на всех марках стали
- с получением твёрдости на подкате и калиброванных прутках из стали марки ЭП 288-Ш
- с образованием трещин на прутках из дисперсионно-твердеющей стали марки ЭП 33-ВД
- с хрупкостью прутков из труднодеформируемой стали марки ЭИ 107.
Для изготовления шестигранных прутков применяли подкат круглого сечения. При контроле качества поверхности подката из всех марок стали была выявлена повышенная загрязнённость его поверхностными дефектами. Поэтому для предотвращения развития поверхностных дефектов при волочении в трещины было решено подвергать прутки подката обязательной обточке до полного удаления дефектов.
Но при изготовлении шестигранных прутков из обточенного подката из стали марок типа 12Х18Н10Т и особенно из трещиночувствительных марок стали ЭИ 961, ЭИ 268 образовывались поперечные надрывы (трещины) (рис. I).
Провели исследование образцов:
- подката после операции обточки;
- калиброванного металла с надрывами после волочения.
В результате проведённого исследования было установлено, что образование трещин при волочении связано с неудовлетворительным качеством поверхности подката после обточки, а точнее с наличием так называемых «гребешков», образующихся в результате грубой механической обработки прутков подката (рис.2). «Гребешки», располагаясь винтообразно по поверхности прутка и поперечно к направлению волочения, служили своего рода концентраторами напряжений, по которым при волочении происходило образование надрывов.
С целью обеспечения надлежащего качества поверхности, то есть удаления «гребешков», а следовательно, для предотвращения образования трещин, подкат после обточки решили подвергать шлифованию.
С введением операции шлифования после обточки качество подготовки поверхности перед волочением значительно возросло и трещины не образовывались. На основании этого обязательное применение обточки и шлифования распространили на подготовку подката из всех нержавеющих высоколегированных марок стали. В качестве химической подготовки поверхности прутков из нержавеющих марок стали использовали щёлочно-кислотное травление металла, которое эффективно способствовало удалению плотной беспористой окалины, образующейся после термической обработки. В процессе освоения технологии изготовления шестигранных прутков наряду с использованием метода щёлочно-кислотного травления было опробовано использование механического способа разрыхления и удаления окалины.
При опробывании вышеуказанного метода были установлены следующие недостатки:
- неравномерность удаления окалины на поверхности прутка (рис.3);
- сложность зачистки шестигранных прутков из-за геометрии профиля
- высокая трудоёмкость и низкая эффективность метода.
Таким образом в результате эксперимента была показана нецелесообразность применения механического способа разрыхления и удаления окалины и низкое качество получаемой поверхности по сравнению с методом щёлочно-кислотного травления. При освоении технологии изготовления шестигранных прутков из стали марки ЭП 288-Ш по ТУ 14-1-759-92 возникли трудности, связанные с обеспечением требуемой твёрдости металла после термической обработки. Опытная технология изготовления прутков предусматривала термообработку металла по режимам, рекомендованным ТУ 14-1-759-92, которая должна была обеспечивать получение твёрдости d отп. ? 3,5 мм и представляла собой следующие режимы для обработки подката и калиброванного металла (таблица 2).
Таблица 2
Режим термической обработки стали марки 07Х16Н6-Ш (ЭП 288-Ш) по ТУ 14-1-759-92
Состояние металла в технологическом процессе |
Режим термической обработки |
||
Технологическая температура, С ? |
Выдержка, час |
Охлаждение |
|
Подкат |
780 680 |
5-6 8 |
по 50 С ?/ч до 600 С ? далее на воздухе воздух |
Калиброванные прутки |
660 + 10 |
8 |
воздух |
Опробывание этих режимов в ТКЦ показало, что стабильного получения регламентированного уровня твёрдости не достигается (d отп.= 3,3-3,7 мм) и особенно на калиброванном металле. Микроструктура стали после термической обработки представлена на рис. 4,5,6,7.
С целью установления причин получения повышенной твёрдости и выбора оптимальных режимов термической обработки в лабораторных условиях были отобраны образцы подката и калиброванного металла. В результате проведённого исследования и на основании литературных данных[ 1] было установлено, что причиной неудовлетворительной твёрдости является образование при холодном волочении мартенсита деформации, так как сталь относится к аустенито-мартенситному классу.
Изменяя температурно- временные параметры процесса термической обработки и используя опыт завода «Серп и Молот» опробовали ( в лабораторных условиях ТКЦ) несколько режимов термообработки подката и калиброванного металла. В результате проведённых экспериментов были разработаны режимы термической обработки ( подката и калиброванного металла), обеспечивающие удовлетворительную твёрдость( d отп.= 3,6-3,8мм) и микроструктуру стали. Которая представлена на рис. 8,9 (таблица 3).
Таблица 3
Разработанный режим термической обработки стали марки 07Х16Н6-Ш (ЭП 288-Ш), обеспечивающий твёрдость d отп. ? 3,6мм.
Состояние металла в технологическом процессе |
Режим термической обработки |
||
Технологическая температура, С ? |
Выдержка, час |
Охлаждение |
|
Подкат |
780 600 |
5-6 8 |
50 С ?/ч до 600 С ?, выдержка 3ч. далее на воздухе воздух |
Калиброванный металл |
600 |
8 |
воздух |
Освоение технологии производства нагартованных прутков шестигранного профиля из дисперсионно-твердеющей стали марки 10Х11Н23МР-ВД (ЭП 33ВД) было связано с особыми трудностями.
Опытная технология изготовления прутков включала в себя следующие основные операции: - термическая обработка для умягчения подката в камерной печи при t 1050 С ?, выдержка 1.0-1.5 часа, с охлаждением в воде;
- щёлочно-кислотное травление прутков для удаления окалины и подготовки поверхности к волочению;
- обточка и шлифование прутков с целью удаления поверхностных дефектов;
- холодное волочение прутков с обжатиями: на первой протяжке-2мм, на последующих протяжках-1мм;
- рекристаллизационный отжиг калиброванных прутков в промежуточных размерах в камерной печи по вышеуказанному режиму.
Используя данную технологию при изготовлении пробных партий прутков размером «под ключ» 10 и 14мм получили повышенную отбраковку по трещинам. Исследованием дефектных образцов установили, что образование трещин, классифицируемых как трещина напряжения (рис.10), связано с природной склонностью стали к дисперсионному твердению и выделению интерметаллоидной фазы при медленном нагреве нагартованного (после волочения) металла.
Было установлено, что рекристаллизационный отжиг, проводимый в камерной печи, способствовал максимальному развитию процессов дисперсионного твердения, и соответственно усиливал трещинообразование. По результатам исследования сделали вывод о необходимости проведения высокотемпературного нагрева прутков после волочения со скоростью, превышающей процесс дисперсионного твердения.
С учётом вышеуказанного была опробована опытная технология изготовления прутков размером «под ключ» 14,17 и 19мм, включающая в себя следующие особенности:
- форсированный нагрев прутков подката в камерной печи до t 1050 С ?, выдержкой 1,0-1,5 ч. С последующим охлаждением на воздухе;
- рекристаллизация (закалка) калиброванных прутков на 4-ой линии ТВЧ при температуре1020- 1060 С ?;
- регламентированная передача калиброванных прутков на рекристаллизацию в течении времени не превышающего 4 часов.
- Изготовление прутков осуществлялось по следующей схеме:
- шестигранник 14мм: круг 19,30мм ( ??) круг 18,60мм (?)шестигранник 17мм (о)?шестигранник 15мм (о)?шестигранник 14мм;
- шестигранник 17мм: круг 22,50мм ( ??) круг 21,60мм (?)шестигранник 20мм (о)?шестигранник 18мм (о)?шестигранник 17мм;
- шестигранник 19мм: круг 24,50мм ( ??) круг 23,80мм (?)шестигранник 22мм (о)?шестигранник 20мм (о)?шестигранник 19мм;
- Где: - ( ??)- обточка и шлифование;
- (?)- волочение;
- (о)- рекристаллизация (закалка) на 4-ой линии ТВЧ.
- В процессе изготовления и при разбраковке готовых прутков установлено следующее:
- после термической обработки при 1050 С ? с охлаждением на воздухе подкат умягчается до d отп. 4,8-5,0мм;
- скоростной индукционный нагрев нагартованных прутков обеспечивает удовлетворительное разупрочнение металла до d отп. 4,6-4,7мм.
- Техническая возможность 4-ой линии ТВЧ позволяет реализовать обработку с нагревом ТВЧ для прутков размером «под ключ» до 19мм включительно, для термообработки прутков размером «под ключ» более 19мм необходимо восстановление линии ИТ 1500/8;
- отбраковки по трещинам не было, качество металла было удовлетворительным и соответствовало требованиям НТД.
Одной из самых сложных в освоении изготовления шестигранных прутков явилась труднодеформируемая сталь мартенситного класса марки 40Х10С2М (ЭИ 107). С самого начала освоения технологии и на протяжении всего времени изготовление шестигранника из этой стали сопровождалось повышенной хрупкостью металла, приводимой к образованию трещин и впоследствии к ломке прутков. Разрушение металла происходило не только при волочении, но и при правке прутков после термической обработки.
По результатам собственного исследования низкой пластичности металла и на основании многочисленных литературных данных [2,3] было установлено, что такое поведение металла обусловлено появлением хрупкости и высокой чувствительностью к образованию трещин (надрывов за счёт напряжений, возникающих при холодной деформации, тем более прутков сложного профиля.
Учитывая это обстоятельство опробовали:
- разные режимы термической обработки подката и калиброванного металла (таблица 4);
- правку прутков в тёплом состоянии;
- разные маршруты волочения, с обжатием за один проход от 0,5 до 2мм.
Таблица 4
Режимы термической обработки стали марки 40Х10С2М (ЭИ 107).
Состояние металла в технологическом процессе |
Режим термической обработки |
||
Технологическая температура, С ? |
Выдержка, ч |
Охлаждение |
|
Подкат и калиброванный металл |
880 |
6 |
по 50 С?/ч до 600 С?, далее на воздухе |
860 |
8 |
по 30 С?/ч до 600 С?, далее на воздухе |
|
740 |
8 |
вода |
|
830 |
8-10 |
вода |
|
710 |
8 |
с печью до 550 С?, далее на воздухе |
|
950 |
4-5 |
по 50 С?/ч до 700 С?, далее на воздухе |
Практически ни по одному из опробованных вариантов, вне зависимости от получаемой твёрдости (d отп.= 3,7-4,1мм), желаемых результатов получить не удалось, о чём свидетельствовал крайне низкий выход годного металла. Повышение технологической пластичности при волочении, а следовательно увеличение выхода годного металла могло бы быть достигнуто за счёт «тёплого» волочения; такая технология успешно применяется для мотков из стали марки ЭИ 107. Однако реализовать её на цепном волочильном стане не представляется возможным.
В результате произведённой работы :
- определены размеры пруткового подката круглого сечения из нержавеющих марок стали в зависимости от размеров готового шестигранника (таблица 5).
Таблица 5
Диаметр пруткового подката круглого сечения из нержавеющих марок стали в зависимости от размера готового шестигранника.
Размер «под ключ» готового шестигранного прутка,мм |
Диаметр прутка подката, мм |
Размер «под ключ» готового шестигранного прутка,мм |
Диаметр прутка подката, мм |
10 |
13 |
24 |
29 |
11 |
14 |
25 |
30 |
12 |
15 |
26 |
31 |
13 |
16 |
27 |
32 |
14 |
18 |
28 |
33 |
15 |
19 |
29 |
34 |
16 |
20 |
30 |
36 |
17 |
21 |
31 |
37 |
18 |
22 |
32 |
38 |
19 |
23 |
33 |
39 |
20 |
25 |
34 |
40 |
21 |
26 |
35 |
41 |
22 |
27 |
36 |
42 |
23 |
28 |
- |
- |
- разработана промышленная технология изготовления шестигранных прутков из стали марок, указанных в таблице 6. Таблица 6
Перечень марок, изготавливаемых в виде калиброванной шестигранной стали.
Группа |
Марка стали |
Размер «под ключ» готового шестигранника, мм |
1 |
12Х18Н10Т, 12Х18Н9Т,08Х18Н10Т |
10-36 |
2 |
12-40Х13, 14Х17Н2 (ЭИ 268), 07Х16Н6 (ЭП 288), 13Х11Н2В2МФ (ЭИ 961), 09Х16Н4Б (ЭП56) |
10-36 |
3 |
10Х11Н23МР-ВД (ЭП 33ВД) |
10-19 |
В целом технология изготовления прутков шестигранного сечения из высоколегированных нержавеющих марок стали предусматривает следующие основные операции: 1. Термическая обработка пруткового подката в камерных печах со стационарным подом (таблица 7). 2. Щёлочно-кислотное травление прутков для удаления окалины и подготовки поверхности к волочению. 3. Обязательная обточка и шлифование прутков подката перед волочением для полного удаления поверхностных дефектов. 4. Холодное волочение прутков из стали марок: 4.1. группа 1,2 таблица 6 с обжатиями: -на первой протяжке-2мм -на последующих протяжках-1мм. Для прутков из стали марок группы 1 размеров «под ключ» 14-36мм допускается обжатие до 2мм на всех протяжках. 4.2 группа 3, таблица 6 с обжатиями: - на промежуточных протяжках 1-2мм; - на окончательной протяжке 1мм. 5. Рекристаллизационный отжиг калиброванных прутков по режимам приведённым в таблице 7. 6. Правка прутков шестигранного сечения на правильных машинах. Таблица 7
Режимы термической обработки подката и калиброванного металла.
№№ пп |
Марка стали |
Состояние металла в технологическом процессе |
Режим термической обработки |
||
Технологическая температура, С? |
Выдержка, час |
Охлаждение |
|||
1 |
12ХН3А-20ХН3А, АС35Г2,АВ35Г2, А12,АС14 |
Подкат (прутки,мотки) |
680 |
10 |
воздух |
Калиброванные прутки |
680 |
8 |
воздух |
||
2 |
12-20ХН,40ХН2МА, 40ХГНМ |
Подкат (прутки,мотки) |
720 |
7 |
3ч без подачи топлива, 3ч с приоткрытым шибером и на воздухе |
Калиброванные прутки |
680 |
8 |
воздух |
||
3 |
10-70, 12-40ХМ, Ст3, 38ХС, 40ХС, 35-45Х, 20-35ХГСА, 40-50ХН, 30ХГСН2А, 15Х5М |
Подкат (прутки,мотки) |
760 |
5 |
3ч без подачи топлива, 3ч с приоткрытым шибером далее на воздухе |
Калиброванные прутки |
680 |
8 |
воздух |
||
4 |
13Х11Н2В2МФ (ЭИ 961), 14Х17Н2 (ЭИ 268), 09Х16Н4Б (ЭП56) |
Подкат (прутки) |
790 680 |
5-6 10 |
50 С?/ч до 600 С?, далее на воздухе воздух |
Калиброванные прутки |
680 |
10 |
воздух |
||
5 |
12-40Х13 |
Подкат (прутки) |
860 |
6 |
50 С?/ч до 740 С? выд. 4-6 ч, далее на воздухе |
Калиброванные прутки |
720 |
7 |
3ч без подачи топлива и на воздухе |
||
6 |
07Х16Н6 (ЭП288) |
Подкат (прутки) |
780 600 |
5-6 8 |
50 С?/ч до 600 С? выд. 3 ч, далее на воздухе воздух |
Калиброванные прутки |
680 |
8 |
воздух |
||
7 |
12Х18Н10Т, 12Х18Н9Т,08Х18Н10Т |
Подкат (прутки,мотки) |
1020 1050 |
1,5-2 |
вода |
Калиброванные прутки (мотки) |
1020 1050 |
1,5-2 |
вода |
||
8 |
10Х11Н23МР-ВД (ЭП 33ВД) |
Подкат (прутки) |
1050 |
1,0-1,5 |
воздух |
Калиброванные прутки |
1020 1050 |
1,0-1,5 |
воздух |
Примечания:
- термообработку мотков из стали марок, указанных под № 7 производить в высокотемпературной печи №19;
- посадка металла должна осуществляться в прогретую до 900 С? печь, нагрев до 1500 С? производить за 1,5-2 часа.
- Термообработку калиброванных прутков производить на 4-ой линии ТВЧ.
3.2 Уточнение технологических маршрутов волочения шестигранных прутков, поставляемых в нагартованном состоянии.
Появление заказов на поставку прутков шестигранного профиля в нагартованном состоянии с нормированными механическими свойствами и твёрдостью (таблица 8) из стали марок А12 (ГОСТ 1414-75), 20-45 (ГОСТ 1050-88) и других потребовало корректировки действующей технологии производства.
Таблица 8
Нормы механических свойств и твёрдости ( ГОСТ 1050-88, 1414-75).
НТД на поставку |
Марка стали |
Размер,мм |
Механические свойства, не менее |
Число твёрдости НВ,не более |
||
Временное сопротивление на разрыв, кгс/мм2 |
Относительное удлинение,% |
Относительное сужение, % |
||||
ГОСТ 1050-88 |
20 25 30 35 40 45 |
50 55 57 60 62 65 |
7 7 7 6 6 6 |
40 40 35 35 35 30 |
207 217 229 229 241 241 |
|
ГОСТ 1414-75 |
30 и менее Свыше 30 |
52 47 |
7 7 |
- - |
217 217 |
Существующая на данный момент технология изготовления прутков, предусматривающая обжатие на окончательной протяжке 1 мм, не обеспечивала получение требуемых норм по механическим характеристикам и твёрдости в состоянии поставки. Для обеспечения вышеуказанных требований были изменены маршруты волочения и изготовлены опытные партии шестигранных прутков с обжатием на окончательной протяжке 2-3 мм. Контроль механических свойств и твёрдости нагартованного металла в состоянии поставки показал удовлетворительные результаты (таблица 9).
Таблица 9
Результаты контроля механических свойств и твёрдости опытных партий.
Марка стали |
№ плавки |
№ пакета |
Размер «под ключ»,мм |
Механические свойства |
Число твёрдости, НВ |
||
Временное сопротивление разрыву,кгс/мм2 |
Относительное удлинение,% |
Относительное сужение,% |
|||||
20 45 А12 |
200147 208997 309392 |
7101 5297 5493 |
22 22 24 |
54,2 54,1 76,3 74,2 61,1 61,0 |
20,8 19,6 9,2 12,4 17,2 19,2 |
58,7 61,7 46,6 46,9 59,1 61,4 |
170 170 217 217 187 187 |
На основании массового опробования разработанных маршрутов волочения было выбрано оптимальное обжатие на окончательной протяжке -2мм. 3.3 Интенсификация процесса холодного деформирования металла за счёт применения неприводных калибрующих роликовых клетей взамен монолитных волок. 3.3.1 Для интенсификации процесса холодного деформировавния с целью уменьшения затрат и улучшения качества металла при изготовлении мелкопрофильного шестигранника хорошо зарекомендовала себя 4-х роликовая клеть конструкции ЧГТУ (Челябинский государственный технический университет) (рисунок 11). При изготовлении шестигранника в роликовой клети реализуется процесс холодного волочения в сочетании с плющением, то есть деформирование металла осуществляется через роликовую и обычную монолитную волоку (рисунок 12). Таким образом, основная деформация металла происходит в роликовой волоке. А в монолитной придаются точные размеры и окончательно формируется шестигранный профиль. Конструкция роликовой клети позволяет производить настройки калибрующих роликов на необходимый размер шестигранника с обеспечением необходимой степени обжатия и получением правильного шестигранного профиля с допуском под чистовую обработку в монолитной волоке. Первым этапом освоения технологии производства шестигранного профиля с применением роликовой клети было изготовление шестигранных прутков размером «под ключ» 8-10 мм из углеродистой (Ст 3) и конструкционных (ст 10-50) марок стали на комбинированной волочильной линии 2КЛ-40Б. В качестве исходной заготовки использовали мотковой подкат круглого сечения. Опытная технология изготовления прутков шестигранного сечения включала следующие операции: - смягчающая термообработка моткового подката - предварительное волочение (степень обжатия не менее 15%) на волочильном барабане для устранения овальности. - рекристаллизационный отжиг калиброванных мотков в колпаковых электропечах. - окончательное волочение в роликовой клети совмещением плющения и волочения на линии 2КЛ-40Б (размер заготовки перед окончательным волочением равен размеру «под ключ», увеличенному в 1,2 раза); при этом величина чистового обжатия в монолитной волоке должна быть не менее 0,5 мм. Опробование вышеизложенной технологии дало положительные результаты. При контроле качество готовой металлопродукции удовлетворяло требованием НТД. Следующим этапом освоения технологии было изготовление: - прутков шестигранного сечения из автоматных (А12,АС35Г2), конструкционных легированных (35-45Х, 30ХГСА, 15Х5М и др.), нержавеющей (12х18н10т) сталей размером «под ключ» 5-10 мм; - мотков шестигранного сечения размером «под ключ» 4 мм из конструкционной (ст35) и автоматной (А12) стали. Опытная технология изготовления мотков шестигранного сечения предусматривала те же операции. Что и для изготовления прутков. Отличительной особенностью являлось волочение с применением роликовой клети по схеме «из мотка в моток», установленной на волочильном барабане ВСМ1/750. При изготовлении опытных партий прутков и мотков шестигранного сечения качество металла было удовлетворительным и соответствовало всем требованиям НТД. Таким образом, в результате проведённой работы по освоению технологии изготовления мелкопрофильного шестигранника с использованием 4-х роликовой клети разработаны две опытно-промышленные схемы производства: - прутков шестигранного сечения по схеме «из мотка в пруток» на волочильной линии 2КЛ-40Б; - мотков шестигранного сечения по схеме « из мотка в моток» на волочильном барабане ВСМ1/750. Основными операциями технологии изготовления прутков и мотков являются: - смягчающая термическая обработка мотков подката в камерных печах (таблица 7); - обточка (при необходимости) для удаления поверхностных дефектов на бунто-обдирочном станке «Кизерлинг»; - предварительное волочение со степенью обжатия 15-25% на волочильном барабане для устранения овальности и получения правильной геометрии круглого профиля; - рекристаллизационный отжиг калиброванных мотков (таблица 10); - окончательное волочение в роликовой клети совмещением плющения и волочения на волочильной линии 2КЛ-40Б (по схеме «из мотка в пруток») или на волочильном барабане ВСМ1/750 (по схеме «из мотка в моток»), при этом размер заготовки перед окончательным волочением должен превышать размер «под ключ» готового шестигранника в 1,2 раза. Перечень марок стали. Изготавливаемой в виде прутков и мотков шестигранного сечения и размеры моткового подката круглого сечения, применяемого для их производства приведены в таблицах 11,12. Таблица 10 Режимы рекристаллизационного отжига калиброванного металла (мотки) в колпаковых электропечах.
№№ пп |
Марка стали |
Диаметр, мм |
Режим термической обработки |
||
Технологическая температура, С? |
Продолжительность выдержки,ч |
Охлаждение |
|||
1 |
А12,АС35Г2, 10-70, Ст.3, АВ35Г2 |
?8 ?8 |
680 680 |
4 6 |
1 час под муфелем и на воздухе |
2 |
20-35ХГСА, 35-45Х,АС14 |
?8 ?8 |
720 720 |
4 6 |
1 час под муфелем и на воздухе |
3 |
38ХС, 40ХС, 12-50ХН |
?8 ?8 |
680 680 |
5 7 |
1 час под муфелем и на воздухе |
4 |
15Х5М |
все диаметры |
680 |
5 |
1 час под муфелем и на воздухе |
Таблица 11
Перечень марок стали, изготавливаемой в виде прутков и мотков шестигранного сечения.
№№ пп |
Марка стали |
Размер «под ключ», мм |
Вид готовой продукции |
1 |
Ст.3, 10-70, 35-45Х, 12-50ХН, 38-40ХС, 20-35ХГСА, 15Х5М,АС35Г2, АВ35Г2, А12, АС14 |
5-10 |
Прутки, мотки |
2 |
12Х18Н10Т, 12Х18Н9Т, 08Х18Н10Т |
5-10 |
Прутки |
Таблица 12
Диаметр моткового подката в зависимости от размера готового шестигранника.
Размер «под ключ» готового шестигранника, мм |
Диаметр моткового подката, заказываемого без учёта операции обточки, мм |
Диаметр моткового подката, заказываемого с учётом операции обточки, мм |
5 6 7 8 9 10 |
8 8 10 11 12 13 |
8 9 10 12 13 14 |
Примечание: для промежуточных размеров готового шестигранника, не указанных в настоящей таблице, размер подката выбирается по ближайшему большему размеру готового шестигранника. 3.3.2 Освоение новой технологии изготовления шестигранных прутков с применением трёхвалковой роликовой клети усовершенствованной конструкции со специальной профилировкой калиброванных роликов. С вводом в эксплуатацию нового волочильного инструмента - трёхвалковой роликовой клети, было начато освоение технологии изготовления калиброванных шестигранных прутков с её применением. Такая технология изготовления представляет собой холодное волочение в сочетании с плющением, то есть процесс волочения в таком случае осуществляется через ролики и обычную коническую волоку. В роликовой волоке металл подвергается основной деформации, а в конической профиль незначительно утончается и кромкам придаются точные размеры. С учётом имеющегося в наличии комплекта калибрующих роликов с использованием трёхвалковой роликовой клети изготовили опытно-промышленную партию прутков размером «под ключ» 14 мм из стали марки 38ХС. Установку роликовой клети осуществляли в пазы лобовины волочильного стана №2 взамен фильерной доски. После установки клети производили подключение системы подачи технологической смазки. Корпус роликовой клети представляет собой сварную конструкцию, состоящую из передней и задней стенки, а также двух боковин (рисунок 13). Внутри корпуса размещены роликовый узел вертикального ролика и два роликовых узла в П- образных кассетах. Три указанных ролика, соприкасаясь между собой образуют шестигранный калибр (в отличие от 4-х роликовой клети конструкции ЧГТУ), в котором выполняется основная деформация металла. Между задней поверхностью П- образных кассет и внутренней поверхностью боковин корпуса установлены клинья и вставка, которая крепится в корпусе с помощью стяжек. В задней стенке клети располагается монолитная волока. В которой происходит окончательное формирование профиля. Собранная клеть сверху закрыта траверсой и зафиксирована четырьмя гайками. В качестве исходной заготовки использовался подкат круглого сечения диаметром 18+ мм. Изготовление прутков проводили по следующей технологической схеме: 18+ (+) ( ??) 17,8 ( ?) 15,8 (о) ( ?) 14,2 ( ?) 14,0 где: (+)- термическая обработка подката (умягчающая); ( ??)- обточка и шлифование; ( ?)- предварительное волочение через ролики (о)- рекристаллизационный отжиг ( ?)- окончательное волочение через ролики ( ?) –окончательное волочение (доводка) через монолитную волоку. Предварительно подкат подвергали умягчающей термической обработке в камерной печи по действующей технологии. С целью полного удаления поверхностных дефектов и устранения овальности прутков подката применяли обточку (шлифование). Изготовление шестигранных прутков осуществляли за два прохода с промежуточным рекристаллизационным отжигом. В результате первого прохода в трёхроликовой волоке из круглой заготовки формировался черновой подкат в виде стрельчатого шестигранника (рисунок 14А). После рекристаллизационного отжига осуществлялся второй проход через роликовый калибр, где прутки приобретали форму правильного шестигранного профиля с допуском под чистовую обработку; одновременно выполнялось калибрование в монолитной волоке до размеров готового профиля ( рисунок 14 Б, В). Процесс волочения производился при постоянной достаточной подаче технологической смазки перед монолитной волокой через специальное отверстие в траверсе и вставке. При изготовлении опытной партии прутков шестигранного сечения размером «пол ключ» 14 мм с использованием трёхвалковой роликовой клети установлено следующее: - для удовлетворительного формирования шестигранного профиля размер прутка подката круглого сечения с учётом обточки должен превышать в 1,25 раза размер « под ключ» готового шестигранника; - необходимо обязательное применение обточки (шлифования) подката перед деформированием с целью получения прутков с хорошим качеством поверхности и точной геометрией профиля; - при настройке роликового калибра необходимо использование шаблона – прутка длиной 500-600 мм шестигранного профиля соответствующего размера с целью обеспечения оптимальной степени заполнения калибра при волочении- деформация металла при первом (черновом) проходе через калибрующие ролики оказывает значительное влияние на формирование углов и ширины граней профиля; - при холодном волочении в сочетании с плющением достигается равномерная деформация по всему периметру прутка и обеспечивается качественное формирование шестигранного профиля. Изготовление опытно-промышленной партии показало эффективность и перспективность использования способа формирования шестигранного профиля в роликовой клети методом совмещения плющения в роликовом калибре с холодным волочением в монолитной волоке. Для разработки промышленной технологии изготовления прутков шестигранного профиля с широким марочным и размерным диапазоном необходимо дальнейшее освоение роликовой клети. 4.ТЕХНИКО – ЭКОНОМИЧЕСКИЕ ПОКАЗАТЕЛИ. Производство калиброванных прутков и мотков шестигранного сечения из углеродистых, автоматных, конструкционных легированных и нержавеющих высоколегированных марок стали при рентабельности +11% обеспечило получение прибыли комбинату за 10 месяцев 2001 года – 2 634 632 руб. 5.ВЫВОДЫ. 1. Разработана и освоена промышленная технология производства калиброванных прутков шестигранного профиля из нержавеющих марок стали 12-40Х, 14Х17Н2 (ЭИ 268), 07Х16Н6 (ЭП288), 13Х11Н2В2МФ (ЭИ961), 09Х16Н4Б (ЭП56), 12Х18Н10(9)Т, 08Х18Н10Т – размером «под ключ» 10-36 мм. 2. Опробована с положительными результатами технология изготовления шестигранных прутков из стали марки 10Х11Н23Т3МР-ВД (ЭП33-ВД) размером «под ключ» до 19мм включительно. 3. Освоение технологии изготовления холоднотянутых шестигранных прутков из стали марки 40Х10С2М (ЭИ 107) не дало положительных результатов. 4. Показана необходимость применения метода щёлочно-кислотного травления для прутков из нержавеющих марок стали. 5. Установлено, что подкат из нержавеющих марок стали перед волочением необходимо подвергать обязательной обточке и шлифованию. 6. Разработаны технологические маршруты волочения прутков шестигранного сечения, поставляемых в нагартованном состоянии с нормированными механическими свойствами и твёрдостью. 7. Освоена технология производства мелкопрофильного шестигранника размером «под ключ» 5-10 мм, поставляемого в прутках и мотках из углеродистой, конструкционной легированной и нержавеющей типа 12Х18Н10Т марок стали. 8. Получены положительные результаты при опробовании трёхвалковой роликовой клети конструкции «ДСС» для производства прутков шестигранного сечения из конструкционной стали марки 38ХС. 9. По результатам проведённой работы подготовлена технологическая инструкция на производство калиброванных прутков и мотков шестигранного сечения. 10. Производство калиброванных прутков и мотков шестигранного сечения является рентабельным и приносит комбинату прибыль. Рис. 1 Поперечные трещины(надрывы) на прутке шестигранного сечения из стали марки 12Х18Н10Т. Рис.2 «Гребешки» после грубой обточки на шестигранном прутке из стали марки ЭИ 961. Рис.3 Пруток шестигранного сечения из стали марки 12Х18Н10Т после применения механического способа удаления окалины. Рис.4 микроструктура стали 07Х16Н6-Ш (подкат) d отп.=3,7мм (отжиг 780?С, выд. 5-6ч, охлаждение по 50 ?С/ч до 600?С, воздух + отпуск 680?С. выд. 8ч, воздух). Рис.5 микроструктура стали 07Х16Н6-Ш (подкат) d отп.=3,3мм (отжиг 780?С, выд. 5-6ч, охлаждение по 50 ?С/ч до 600?С, воздух + отпуск 680?С. выд. 8ч, воздух). Рис. 6 Микроструктура стали 07Х16Н6-Ш (калиброванный металл) d отп.=3,6мм (отпуск 660?С, выд. 8ч, воздух) Рис.7 Микроструктура стали 07Х16Н6-Ш (калиброванный металл) d отп.=3,4мм (отпуск 660?С, выд. 8ч, воздух) Рис. 8 Микроструктура стали 07Х16Н6-Ш (подкат) d отп.=3,7мм (отжиг 780?С, выд. 5-6ч, охлаждение по 50 ?С/ч до 600?С,выдержка 3ч, воздух + отпуск 600?С. выдержка 8ч, воздух). Рис. 9 Микроструктура стали 07Х16Н6-Ш (калиброванный металл) d отп.=3,6мм ( отпуск 600?С. выдержка 8ч, воздух). рис.10 Трещины на шестигранных прутках из стали марки ЭП33-ВД Рис.11 1- станина , 2- валок, 3- механизм осевой регулировки. Рис.12 1-заготовка, 2- ролик, 3- монолитная волока. Рис.13 1-корпус, 2- кассета, 3- клин, 4- вставка, 5- траверса. Рис. 14 А и Б – первый и второй роликовые калибры, В – монолитная волока. СПИСОК ЛИТЕРАТУРЫ. 1. Е.А. Ульянин. Коррозионностойкие стали и сплавы. М. «Металлургия», 1991г. 2. М.И. Гольдштейн. Специальные стали. М. «Металлургия», 1985 г. 3. Э.А. Гудремон. Специальные стали. М. «Металлургия» 1959 г.